Spinning
Spinning consists of the transformation of raw materials into yarn. The latter can be made of fibers or filaments.
A fiber is a filamentary substance, it is characterized by its discontinuous length.
For some natural plant fibers (such as linen or hamp), the rovings are dipped in hot water at 60 to 70°C to soften the fibers and facilitate spinning.
A filament is extruded by a spinneret, melted for synthetic materials or solubilized for artificial materials, then drawn and cooled for meltspin or coagulated and drawn in the case of the solvent process. The result is a continuous length fiber that is called filament. The filaments are necessarily of chemical origin (synthetic or artificial).
The filaments can be converted into fibers by the action of stretch breaking/cracking (pulling the filament until it breaks) or crush cutting/converting (cutting the filaments).
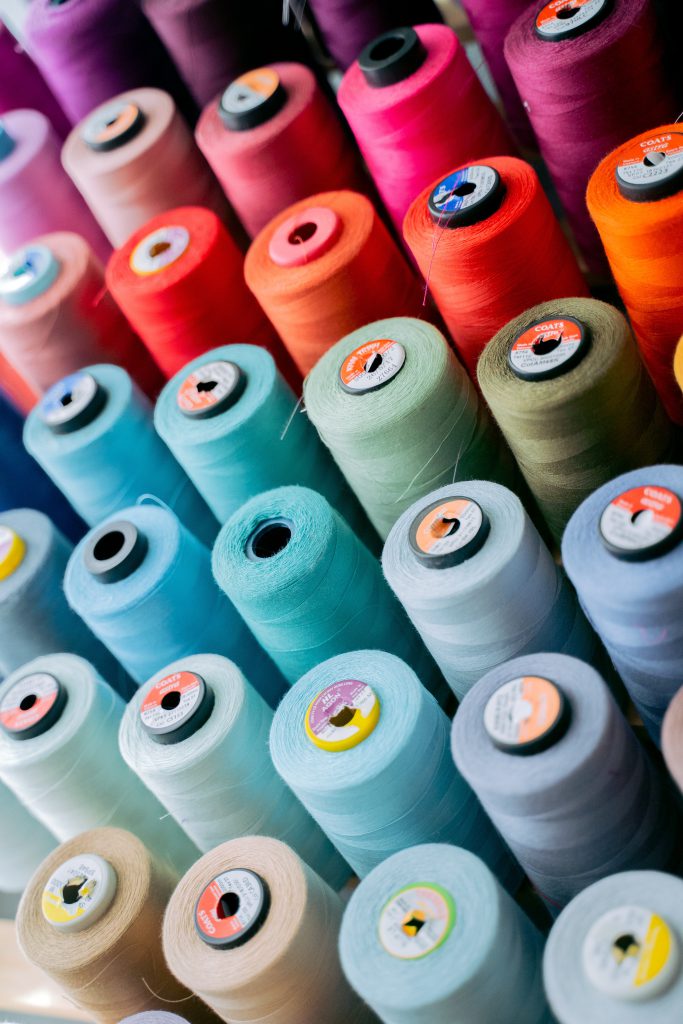
Caractéristiques
A yarn is characterized by its count, defining its fineness. This can be expressed by different quantities : in metric number Nm (Km/Kg), in Dtex (g/10000m) or in Deniers Dn (g/9000m). It is also characterized by its regularity and its homogeneity, which represent the variation of the count along the longitudinal axis measured in cN/Tex (centi Newton / Tex) as well as its direction and coefficent of torsion.
See the different units of measurementTypes of spinning
Conventional spinning
- Fibers preparation : Remove impurities from natural fibers.
- Homogeneization : Organize the flock (cluster of fibers) to obtain a regular batt.
- Carding : Remove the last impurities, untangle and align the fibers to obtain a web or a silver.
- Combing : To increase the quality of the product by eliminating the short fibers and paralleling the remaining fibers. This step is not mandatory.
- Gills : Refine and homogenize, also used for fiber mix. Step to be repeated several times. Allows to obtain a ribbon.
- Flyer frame or rubbing frame : Obtain a twisted roving with the flyer frame, and a flat roving ith a false twist in the case of rubbing frame.
- Ring spinning : Obtaining the yarn by drawing, twisting roving and drafting (winding the yarn obtained on coil).
Unconventional spinning
- Open-end : The fibers of the roving are released and then twisted directly. It is the speed of rotation that induces a centrifugal force, which allows to form the yarn. This technique allows a higher yield anda lower production cost, for a breaking resistance reduced by about 30%.
- Self-twisting : Two roving passed between rubbers that will alternately create right to left movements. This system makes it possible to form S.twists and Z-twists.
- Air jet spinning : A silver is subjected to a jet of compressed air that will cause silver to become thinner and more twisted. It is a technique that allows a high yield and low cost for a less solid yarn and more limited in the choice of the count.
Compound yarn
Once the yarns have been obtained, they can be wound together in different ways in order to provide new technical or aesthetic properties.
- Multifilament : Yarn composed of several filaments with or without twist.
- Plied yarn : Two yarns twisted together (S or Z).
- Cabled yarn : Twisting of several yarns with at least one plied yarn.
- Assembled yarn : Apposition of single, plied or cabled cord yarns without twisting.
- Textured yarn : Crimp or corrugated filaments assembled.
- Fancy yarn : Creation of a yarn with a different esthetic by varying the spinning process, for example by different yarn tensions or thicknesses.
- Covered yarn : Composed by a core yarn on which another yarn is wound to cover it. This technique is used in particular for elastane yarns to preserve their elastic properties, but also in the case of the use of fragile ceramic or carbon yarns for example.