Nonwovens
An entanglement of fibers or filaments, oriented or randomly arranged. Nonwovens are presented in the form of webs, batts or mats.
In order to obtain a better resistance, one can increase its internal cohesion by mechanical, physical or chemical consolidation methods.
There are two categories of nonwovens, disposable and durable.
The disposable ones are thin and not very qualitative, they are intended for the hygiene, medical, filtration and protection fields.
The durable ones are more qualitative and are used in many fields such as automotive, agriculture, civil engineering, etc.
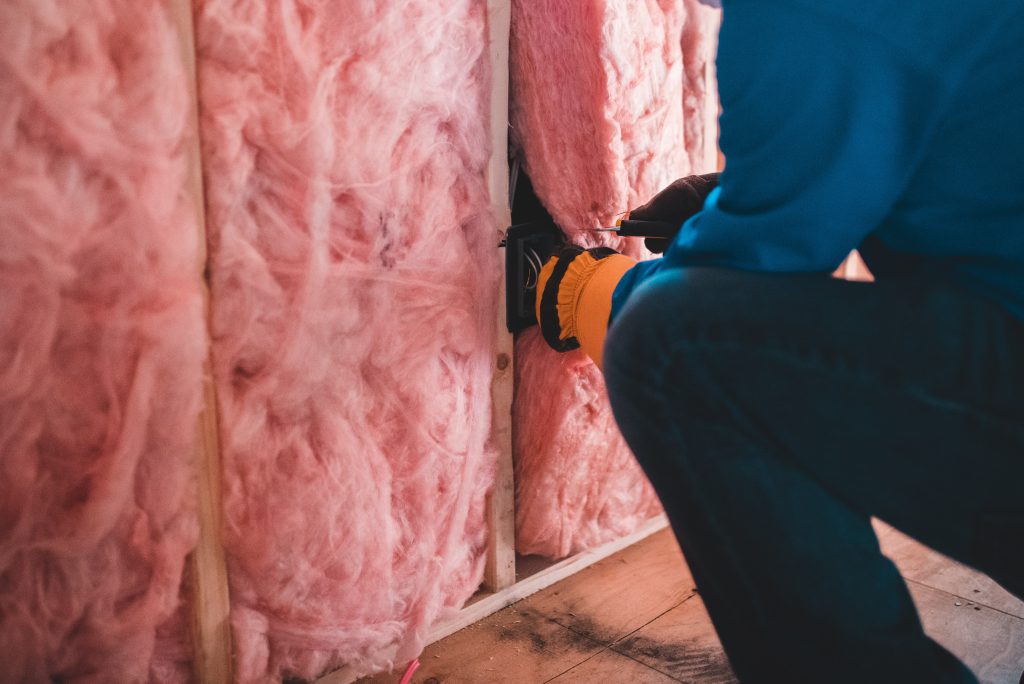
Nonwovens processing
There are several methods for making nonwovens.
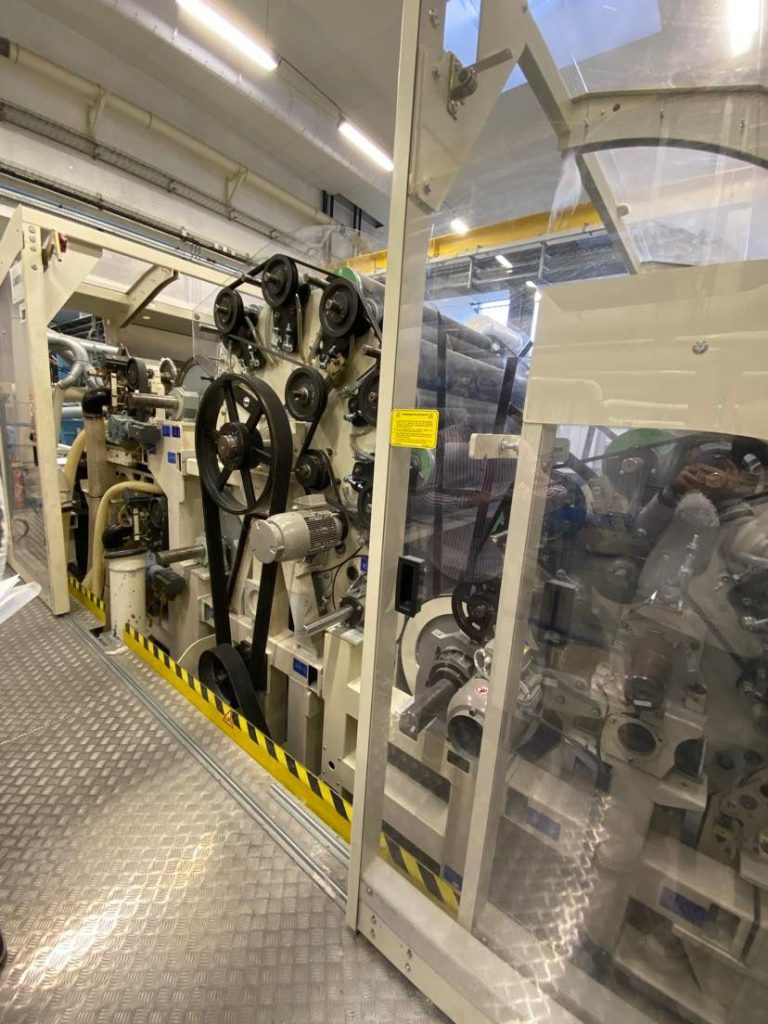
Drylaid
The natural or chemical fibers enter in the form of flock in a carding machine which will allow to disentangle them, to align them and to eliminate the impurities. A veil is obtained at the end of the carding machine, which can then be passed to the topping to increase its thickness.
Airlaid
The fibers, even very short ones, are carried and dispersed in an air stream. This process allows to quickly obtain a batt where the fibers are randomly oriented.
Wetlaid
The fibers are suspended in water, then filtered, sifted, vacuumed and compacted. It allows to obtain a dense web, with very short fibers of cellulosic or synthetic inorganic origin, with a random orientation of the fibers.
Spunmelt
- Extrusion (spunbond) : The chemical polymer is extruded, cooled, then desposited on a mat to form a web. The fibers are bound together by thermal consolidation.
- Blown extrusion (meltblown) : The process is the same as for spunbond, with an additional step of drafting under hot air and then cooling to obtain a finer yarn.
- Electrospinning : The polymer is dissolved in a solvent and then sprayed into a vacuum vessel, allowing instant evaporation of the solvent. The cloud of filaments formed is then consolidated.
Bonding methods
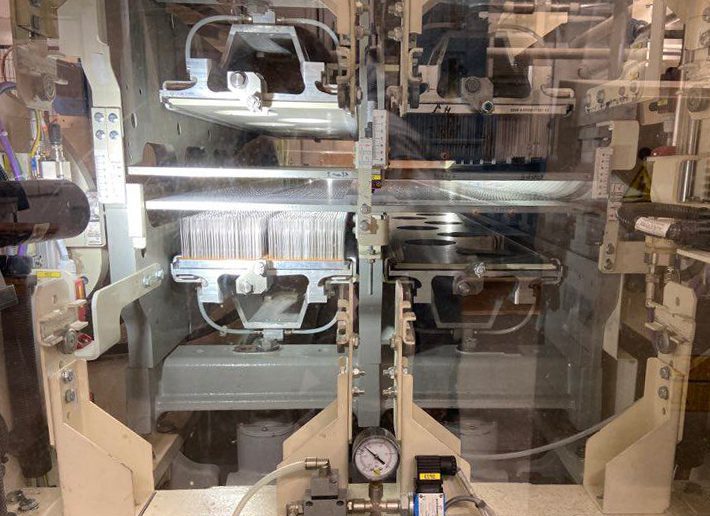
Mechanical bonding by friction
Consolidation which is carried out by the means of one tread or morevia the entanglement of existing fibers. Several methods are used :
- Needlepunching : The material is crossed by hooked needle boards that entangle the fibers from the bottom to the top of the surface in order to increase the bonds and to obtain better mechanical characteristics.
- Hydro-entranglement : The material passes through perforated blades through which water is sprayed at very high pressure to entangle the fibers. This technique increases the cohesion between the fibers and thus provides better mechanical performance. The higher the pressure, the more resistant the material will be, but the more it will suffer a loss of thickness and porosity due to the settling of the material as a result of the pressure (up to about 200 bars).
- Sewing-knitting : The material is sewn with more or less important spacing. There are many different stitches, all of which increase the mechanical strength of the surface.
Thermal bonding
- Thermal bonding is only possible on nonwoven composed of a thermofusible filaments part and a part not thermofusible. The principal consists in bringing the thermofusible filaments to its melting point so that it softens and thus fixes the other fibers. Several techniques are possible such as the oven, the compacting cylinders, the calendering (heating cylinders allowing also to adjust the thickness of the nonwoven) and the ultrasounds.
Chemical bonding
Fixation of the fibers and maintenance of the structure through the use of a chemical binder based on polymers or copolymers. They are applied by impregnation, by spraying or by coating.
Types of materials processed
Mainly synthetic, artificial, natural and mineral.
Characteristics
Pouvoir fortement filtering, power, very porous (important presence of air), low resistance (the resistance increases with the bonding methods), speed of production, etc.
Applications
Hygiene (diapers, sanitary towels), tea bag, packaging, medical, automotive equipments, manufcture of material for composites, buildings etc.