Les nontissés
Enchevêtrement de fibres ou de filaments, orientés ou disposés au hasard. Les nontissés se présentent sous forme de voiles, de nappes ou encore de matelas.
Afin d’obtenir une meilleure résistance, on peut augmenter sa cohésion interne par des méthodes de consolidations mécaniques, physiques ou chimiques.
Il existe deux catégories de nontissés, les jetables et les durables.
Les jetables sont fins et peu qualitatifs, ils sont à destination du domaine de l’hygiène, du médical, de la filtration et de la protection.
Les durables eux sont plus qualitatifs et sont utilisés dans de nombreux domaines tels que l’automobile, l’agriculture, le génie civil, etc…
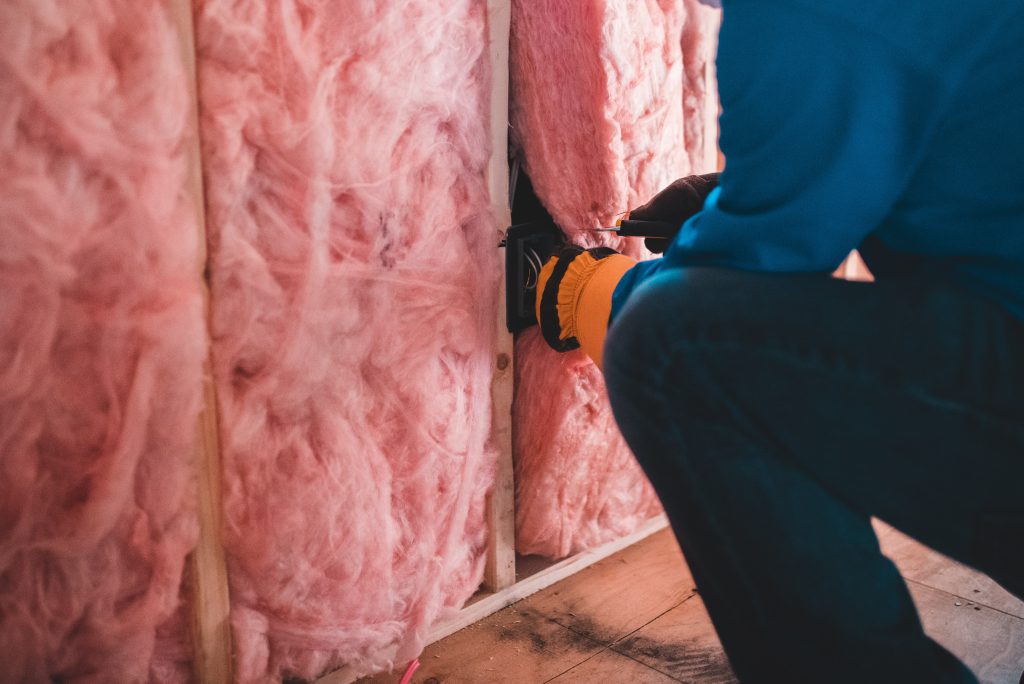
Mode de formation
Il y a plusieurs méthodes pour la mise en œuvre de nontissés.
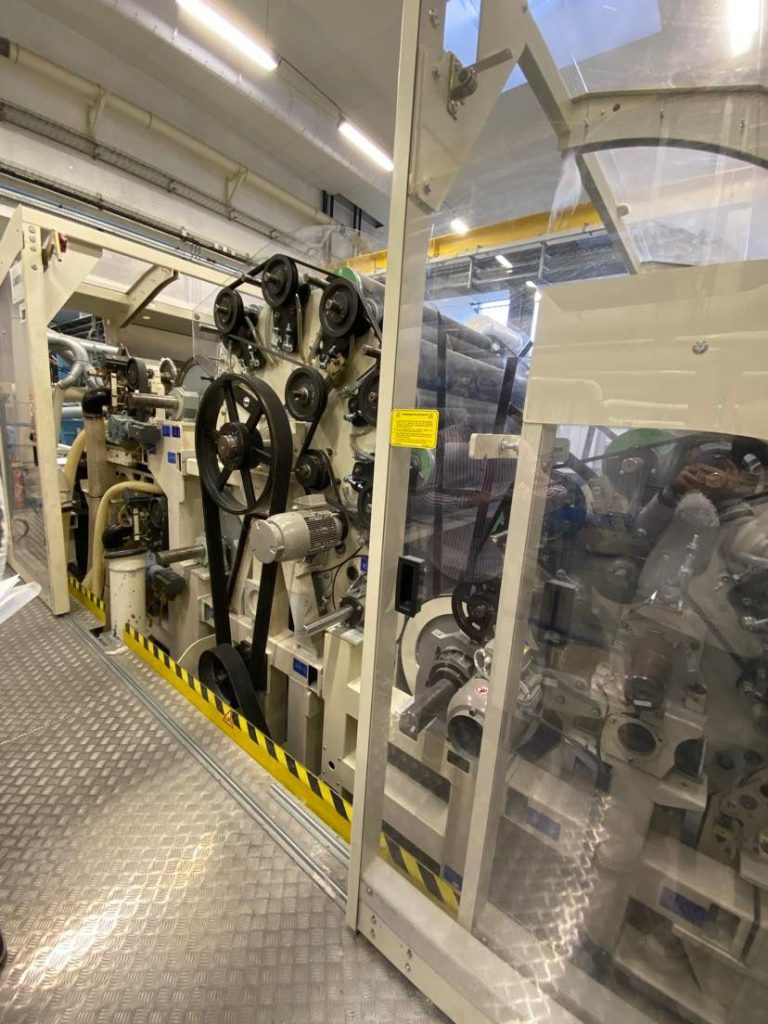
Par voie sèche
Les fibres d’origine naturelle ou chimique entrent sous forme de bourre dans une carde qui va permettre de les démêler, de les aligner et d’éliminer les impuretés. On obtient un voile en sortie de carde, qui peut ensuite être passé au nappage pour augmenter son épaisseur.
Par voie aérodynamique
Les fibres, même très courtes, sont véhiculées et dispersées dans un flux d’air. Ce processus permet d’obtenir rapidement une nappe où les fibres sont orientées aléatoirement.
Par voie humide
Les fibres sont en suspension dans l’eau, elles sont ensuite filtrées, tamisées, aspirées puis compactées. Permet d’obtenir un voile dense, avec des fibres très courtes d’origine cellulosique ou synthétique inorganique, avec une orientation aléatoire des fibres.
Par voie fondue et solvante
- Extrusion (spunbond) : Le polymère de nature chimique extrudé, refroidi, puis déposé sur un tapis afin de former un voile. Les fibres se lient grâce à une consolidation
- Extrusion soufflée (meltblown) : Le principe est le même que pour le spunbond, avec une étape supplémentaire d’étirage sous air chaud puis de refroidissement permettant l’obtention d’un fil plus fin.
- L’électrofilage : Le polymère est dissout dans un solvant puis pulvérisé dans un récipient sous vide, permettant l’évaporation instantanée du solvant. Le nuage de filaments formé est ensuite consolidé.
Les méthodes de consolidations
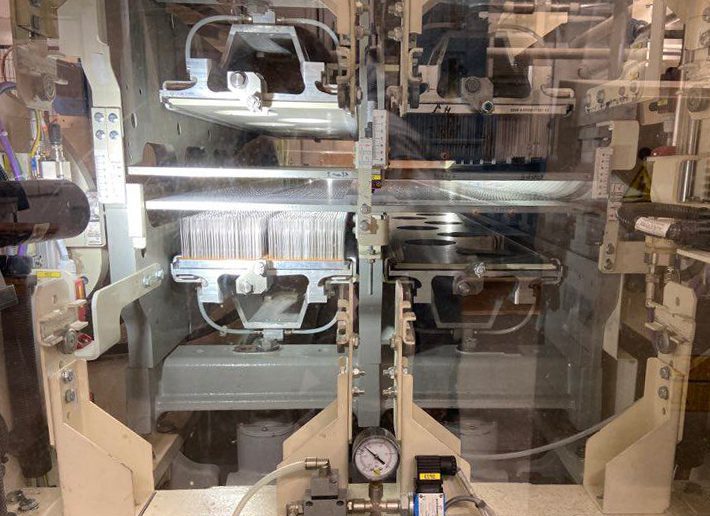
Mécaniques par friction
Consolidation qui s’effectue par l’enchevêtrement de fibres ou par l’ajout de fils. Plusieurs méthodes sont utilisées :
- L’aiguilletage : La matière est traversée par des planches d’aiguilles à crochets qui viennent emmêler les fibres de bas en haut de la surface afin d’augmenter les liens et d’obtenir de meilleures caractéristiques mécaniques.
- L’hydroliage : La matière passe sur des lames perforées au travers desquels de l’eau est projetée à très haute pression afin d’emmêler les fibres entre elles. Cette technique permet d’augmenter la cohésion entre les fibres et ainsi d’obtenir de meilleures performances mécaniques. Plus la pression est importante, plus le matériaux sera résistant, mais plus il subira une perte d’épaisseur et de porosité dû au tassement de la matière, conséquence de la pression (jusqu’à 200 bars environ).
- La couture-tricotage : La matière est cousue avec des espacements plus ou moins importants. Il existe de nombreux points variés, tous permettent d’augmenter la tenue mécanique de la surface.
Thermiques
Consolidation thermique possible que sur des nontissés composés d’une partie de filaments thermofusibles et une partie non thermofusibles. Le principe consiste à amener la fibre thermofusible à son point de fusion afin qu’elles ramollissent et ainsi fixe les autres fibres. Plusieurs techniques sont possibles comme le four, les cylindres compacteurs, le calandrage (cylindres chauffants permettant aussi de régler l’épaisseur du nontissé) et les ultrasons.
Chimiques
Fixation des fibres et de maintien de la structure grâce à l’utilisation d’un liant chimique à base de polymères ou copolymères. Ils sont appliqués par imprégnation, par pulvérisation, ou par enduction.
Type de matières traitées
Principalement synthétiques, artificielles, naturelles et minérales.
Caractéristiques
Pouvoir fortement filtrant, très poreux (présence importante d’air), peu résistant (la résistance augmente avec les méthodes de consolidations), rapidité de production, etc.
Applications
Hygiène (couches, serviettes hygiéniques), sachet de thé, emballages, médical, équipement automobile, fabrication de matière pour les composites, bâtiments etc.